Immer mehr Unternehmen wollen die Vorteile von Lithium-Ionen-Batterien in Gabelstaplern und Lagertechnikgeräten für ihre Intralogistikprozesse nutzen. Doch ist das auch in temperaturgeführten Umgebungen, zum Beispiel in Kühlhäusern bei arktischen Temperaturen, möglich? Wie kann die Leistungsfähigkeit von Lithium-Ionen-Batterien auch bei Kälte und Temperaturschwankungen erhalten werden?
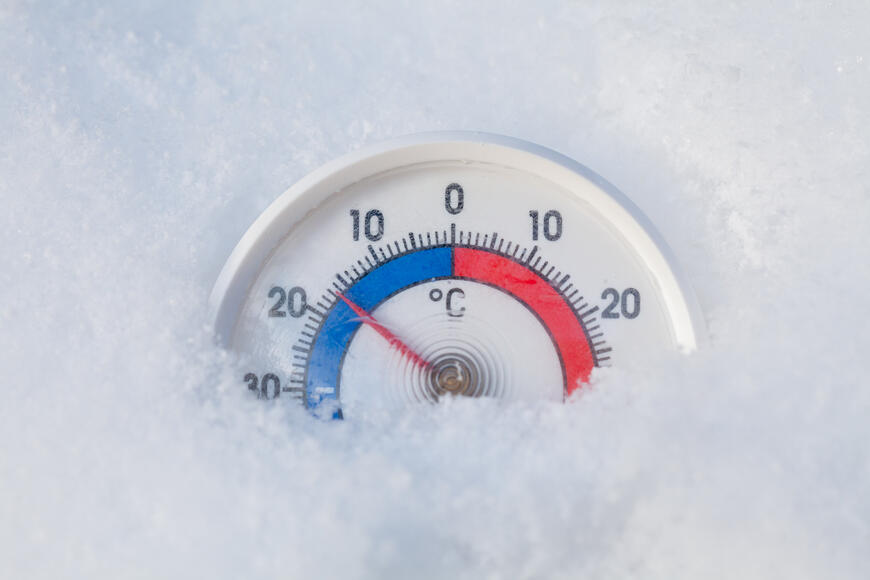
Die energieeffiziente Lithium-Ionen-Technik punktet bei Betreibern und Fahrern aus vielerlei Hinsicht. Lithium-Ionen-Batterien ermöglichen einen Mehrschichtbetrieb ohne den sonst üblichen Batteriewechsel und die Kosten für Wechselbatterien. Pausen und Stillstandszeiten werden genutzt, um die Batterien – wann immer es möglich ist – durch kurze Zwischenladungen schnell mit Energie zu versorgen. Die Batterien werden nicht mehr alle gleichzeitig, sondern über den Tag verteilt, geladen. Dadurch wird wertvolle Zeit für den Wechselvorgang eingespart. Zudem sorgt intelligentes Lademanagement dafür, teure Stromspitzen zu vermeiden.
Durch Lithium-Ionen-Batterien lassen sich zudem Energiekosten einsparen und CO2-Emissionen senken. Die Batterien speichern die zugeführte Energie mit sehr geringen Verlusten und erreichen dadurch einen Wirkungsgrad von über 95 Prozent. Die leichteren Lithium-Ionen-Batterien reduzieren das Gesamtgewicht der Geräte, wodurch der Energieverbrauch um bis zu 21 Prozent geringer ausfallen kann. Auch auf den Verschleiss, z. B. von Rollen, hat das geringere Gesamtgewicht einen positiven Effekt. Für weitere Informationen zur Optimierung der Energie- und CO2-Bilanz Ihrer Staplerflotte empfehlen wir unseren Blog Beitrag "Fünf Schritte zu einer nachhaltigen Intralogistik".
Ein weiteres Plus für den Anwender: Im Gegensatz zu herkömmlichen Blei-Säure-Batterien kommt es bei Flurförderzeugen, die mit Lithium-Ionen-Batterien betrieben werden, zu keinem Leistungsabfall im Laufe des Einsatzes. Die Energie wird gleichmässig abgegeben und während der Rekuperation aufgenommen. Und das nahezu unabhängig von der Restkapazität. Fahrer loben immer wieder die konsequent hohe Leistung der mit Lithium-Ionen-Batterien betriebenen Geräte - insbesondere im hektischen Logistikalltag.
Da liegt es auf der Hand, diese Technologie auch für die zeitkritischen Prozesse in der Lebensmittellogistik zu nutzen. In der Branche wird zwischen dem Trockensortiment, Frischware und Tiefkühlware unterschieden. Während das Trockensortiment bei normalen Raumtemperaturen gelagert wird, müssen Waren aus dem Frischesortiment, wie Molkereiprodukte, Wurst, Frischfleisch und frischer Fisch aber auch Obst und Gemüse, temperaturgeführt bei 2 bis 4 oder 8 Grad Celsius gelagert werden. Dabei weisen diese Produkte in der Regel eine kurze Haltbarkeit auf und müssen daher in kürzester Zeit umgeschlagen werden. Tiefkühlkost und Eis lagern gar bei frostigen Temperaturen von -18 Grad Celsius und kälter.
Tiefkühl-Einsätze – eine Herausforderung für Gerät und Batterie
Für die Lagerung und den Transport unter diesen extremen Temperaturbedingungen bietet der Markt spezielle Gabelstapler und Lagertechnikgeräte in sogenannter Kühlhausausführung an. Für den Fahrer bieten beheizbare Kabinen einen komfortablen Arbeitsplatz. Die Geräte entsprechen den Hygienevorschriften und sind mit einem speziellen Korrosionsschutz ausgestattet. Verlassen die Geräte zum Laden den Kühlbereich oder durchqueren verschiedene Temperaturzonen, so kann es zur Bildung von Kondenswasser oder Eis kommen. Der Korrosionsschutz sorgt dafür, dass die unerwünschte Entstehung von Rost bzw. eine zu hohe Belastung der Technik und Elektronik vermieden wird.
Zu den generellen Massnahmen zum Schutz von Gerät und Technik zählen:
- mehrfach kontrollierte Schweissnähte,
- verzinkte Ausführungen von Metallteilen,
- einzelne Bauteile oder Gerätechassis aus Edelstahl,
- Isolierung der Leitungen,
- Verkapselung der Elektronik,
- Verwendung von speziellem Kühlhausöl,
- Wärmeschutz oder Batterieheizung für die Batterie.
Minusgrade und hohe Temperaturunterschiede setzen jedoch nicht nur dem Gabelstapler zu. Batterien entladen sich bei niedrigen Temperaturen schneller und verlieren so an Leistung. Generell gilt, je niedriger die Temperatur, desto geringer die Batteriekapazität. Bei einer Elektrolyt-Temperatur von 30 Grad Celsius ist die Kapazität einer Blei-Säure-Batterie am grössten, bei -20 Grad Celsius Elektrolyt-Temperatur sinkt die verfügbare Kapazität bis auf 55 Prozent. Auch das Laden dauert bei niedrigen Temperaturen im einstelligen Bereich länger, weil die Batterie die Energie schlecht aufnehmen kann und ist bei Minustemperaturen gar unmöglich. Daher müssen Blei-Säure-Batterien bei herkömmlichen Raumtemperaturen gelagert und geladen werden. Bei Tiefkühleinsätzen werden deshalb meist zwei Wechselbatterien, also drei Blei-Säure-Batterien pro Gerät benötigt. Ausserdem ist der Instandhaltungs- und Pflegeaufwand für Blei-Säure-Batterien im Tiefkühleinsatz höher. Etwa um sogenannte Kriechströme und damit Entladungen zu vermeiden, die durch Feuchtigkeit und Schmutz auf der Oberfläche begünstigt werden.
Vorteile des Lithium-Ionen-Einsatzes im TK-Bereich
Ist der Einsatz von Lithium-Ionen-Akkus in Kühl- oder Tiefkühl-Umgebungen überhaupt wirtschaftlich möglich? Oder sind Kapazitätsverluste und damit eine Verkürzung der Batterie-Lebensdauer zu befürchten? Was viele Flottenbetreiber noch nicht wissen, auch unter extremen Umgebungsbedingungen ist der Einsatz von Lithium-Ionen-Batterien in mehrfacher Hinsicht sinnvoll. Das von Toyota produzierte Batteriesystem ist speziell auf die Bedürfnisse von Flurförderzeugen ausgelegt und auch in einer Kühlhaus-Version erhältlich. Das System unterscheidet sich von üblichen Akkus aus Privatanwendungen durch eine bedeutend robustere Konstruktion, eine hohe Qualität der einzelnen Zellen und Module sowie aufwendigere Sicherheitskomponenten. So ist jedes einzelne Modul und auch das Batteriesystem als Ganzes gegen Staub und Spritzwasser geschützt. Das in sich geschlossene System ist absolut wartungsfrei und setzt weder während des Ladens noch im Betrieb Gase an die Umwelt frei. Somit entfällt eine spezielle Belüftung des Ladebereichs und Bediener müssen kein Wasser auffüllen oder gar mit Säure hantieren.
Durch die Schutzhülle und die während des Betriebs entstehende Wärme kühlt das Toyota Batteriesystem nicht so schnell aus und funktioniert auch im Standard bei niedrigen Temperaturen. Die Kühlhaus-Version verfügt darüber hinaus über ein Thermomanagementsystem, das die Temperatur innerhalb der Zellen eines Moduls überwacht. Wird ein Modul innerhalb der Lithium-Ionen-Batterie zu kalt, erhält der Fahrer eine Meldung, die ihn darauf hinweist, in eine wärmere Umgebung zu fahren. So kann das Gerät bei -10 °C bis zu 4 Stunden und bei -30°C bis zu 2 Stunden ohne Batterieheizung betrieben werden. Soll das Gerät permanent im Kühlhaus eingesetzt und sogar dort geladen werden, ist die Batterie in der Kühlhaus-Version auch mit einer Heizung erhältlich.
Durch den permanenten Verbleib des Gerätes im Tiefkühlbereich lassen sich viele Vorteile erzielen:
- keine beschlagenen Scheiben,
- Vermeidung von Korrosion,
- Reduzierung der Belastungen auf Maschine und Material allgemein, insbesondere auf die Dichtungen und die Batterie
Deshalb sollten Betreiber die Logistikprozesse aber auch die Ladeprozesse so gestalten, dass Temperaturwechsel für den Stapler samt Batterie vermieden werden. Dazu überwacht das integrierte Thermomanagement-System die Temperatur und die Spannung in den einzelnen Batteriemodulen und hält diese mithilfe der Batterieheizung konstant im optimalen Temperaturbereich.
Das von Toyota Material Handling angebotene Batteriesystem arbeitet äusserst energieeffizient. Erst wenn ein Modul eine zuvor definierte Temperatur unterschreitet, aktiviert sich die Batterieheizung. Dadurch wird verhindert, dass die Batterie zu kalt wird und somit an Kapazität verliert. Das wirkt sich positiv auf die Verfügbarkeit und die Betriebskosten aus und erhöht die Lebensdauer der Geräte. Dank des Thermomanagements und der Batterieheizung kann der Stapler permanent im Tiefkühlbereich bleiben, selbst bei Temperaturen bis -30 Grad Celsius. Den Mehrkosten für den erhöhten Energieverbrauch stehen dabei Einsparungen durch den reduzierten Verschleiss von Batterie und Gerät gegenüber.
Um die Lithium-Ionen-Batterien auch im Kühlbereich laden zu können, sollte das Ladegerät samt Kabel zum Schutz vor der Kälte eingehaust werden oder in einem wärmeren Bereich mit mindestens + 5 °C verbleiben und nur zum Laden über ein entsprechend langes Kabel mit dem im Tiefkühlbereich befindlichen Gerät verbunden werden. Der speziell für häufiges Ein- und Ausstecken konstruierte Toyota-Stecker lässt sich dafür auch mit Handschuhen sehr einfach bedienen.
Damit sprechen viele Gründe für den Tiefkühl-Einsatz von Lithium-Ionen-Batterien in Flurförderzeugen:
- Höhere Energieeffizienz und geringe CO2-Emissionen
- Einfache und sichere Handhabung
- Kürzere Ladezeiten
- Keine Wechselbatterien nötig
- Wartungsfreiheit und keine Ausgasungen beim Laden oder im Betrieb
- Thermomanagement-System überwacht die Temperatur jeder einzelnen Zelle innerhalb der Batterie
- In jedes Modul integrierte und nur bei Bedarf aktivierte Batterieheizung schützt die Zellen vor Auskühlung
- Lithium-Ionen-Batterien lassen sich im Tiefkühlbereich und beliebig oft zwischenladen
- Absolut sicheres System mit hoher Verfügbarkeit
Die Batteriegrösse und damit die Investitionskosten für Lithium-Ionen-Batterien kann Toyota bei einer detaillierten Einsatzanalyse und mithilfe des Batterierechners vorab für jeden Einsatz berechnen. Kann ein Gerät während des Einsatzes öfter zwischengeladen werden, kann der Betreiber eine kleinere und damit kostengünstigere Batterie einsetzen. Unterschiede gibt es auch bei Ladegeräten, da Lithium-Ionen-Batterien sowohl mit niedrigen als auch mit hohen Ladeströmen geladen werden können. Generell gilt: Je besser der Einsatz analysiert und der tatsächliche Energiebedarf über den Tag bestimmt wird, umso besser kann das passende Gerät, die benötigte Batteriekapazität und das passende Ladegerät ermittelt werden.
In dieser Form einzigartig bietet Toyota für sein Batteriesystem eine erweiterte Kapazitätsgarantie: 5 Jahre mindestens 80 %, 6 Jahre mindestens 70 %, 7 Jahre mindestens 60 %. Damit hat der Betreiber eine hohe Sicherheit für seine Planung.
Mit dem Toyota Batteriesystem...
- ... schliessen Sie Fehlbedienungen bei der Handhabung aus.
- ... verbessern Sie die Arbeitssicherheit.
- ... reduzieren Sie Ihre Gesamtkosten.
- ... sparen Sie Energie.
- ... reduzieren Sie den CO2 Ausstoss.
In der Praxis: Wie Lithium-Ionen-Stapler beim Energie sparen helfen
Schnelligkeit in der Be- und Entladezone, die Einhaltung der Kühlkette für die angelieferten Lebensmittel und das Thema Energieeinsparung sind die wichtigsten Herausforderungen für das Tiefkühl Frischecenter in Emstek. „Kühlen kostet Geld, daher muss die Kälte auch beim Be- und Entladen der LKWs im Kühlhaus bleiben“, erklärt Standortleiter Guido Selonke. Das gerade erst im Mai 2020 eröffnete Lager ist nach hohen Energieeffizienzstandards und dem Haus-in-Haus-Konzept gebaut. Damit ist die Isolationsschicht des Kühlhauses keinen direkten Witterungseinflüssen ausgesetzt und heizt sich vor allem im Sommer nicht so stark auf.
Den Stromverbrauch gering zu halten, war auch ein wichtiges Thema bei der Auswahl der Flurförderzeuge inklusive der benötigten Batterien und der Ladeinfrastruktur. Neben dem Tiefkühl-Palettenlager (- 18°C) und Frischebereichen (von 2 bis 8 °C) verfügt das Kühlhaus über einen grosszügigen Tiefkühl-Verladebereich mit Abstellflächen, um mehrere LKW gleichzeitig abfertigen zu können. Mit Hilfe der Toyota BT Levio Niederhubwagen mit extra langen Gabeln, der Toyota BT Staxio Doppelstock-Hochhubwagen sowie des Toyota Traigo 48 Elektrostaplers werden selbst grosse Sattelauflieger in kürzester Zeit be- oder entladen. Über zwei Förderstrecken ist der Verladebereich mit dem Tiefkühllager verbunden. Die Ein- und Auslagerung in die über 12 m hohen Regale übernehmen die Mitarbeiter mit zwei Toyota BT Reflex Schubmaststaplern.
Betreut wird das Tiefkühlhaus durch Schlüter Gabelstapler, Teil des Händlernetzwerks von Toyota Material Handling. Die gesamte Flotte ist speziell für den Kühlhauseinsatz ausgestattet und ist mit einem Full Service Vertrag gemietet. Doch während Flurförderzeuge im Kühlhaus bisher mit klassischen Blei-Säure-Batterien betrieben wurden, sind die Flurförderzeuge im Tiefkühl Frischecenter mit dem energieeffizienteren Toyota Batteriesystem unterwegs. „Ich habe viele Jahre Erfahrung mit normalen Blei-Akkus und war anfangs sehr kritisch. Lithium-Ionen-Akkus mit Batterieheizung, die wiederum Strom braucht – das kann ja nicht funktionieren. Ich bin aber eines Besseren belehrt worden“, erinnert sich Selonke, denn:
„Es funktioniert tatsächlich und es funktioniert sehr gut und ist wesentlich energieeffizienter!“
Die Heizung im Toyota Batteriesystem wird nur eingeschaltet, wenn die Batterie zu kalt wird. Das ist im regulären Betrieb aber kaum der Fall, sondern nur, wenn das Gerät in der Kälte steht. Das belegen auch intern durchgeführte Messungen von Toyota Material Handling. Daher profitiert der Kühlhausbetreiber im Praxiseinsatz von den allgemeinen Vorteilen der Lithium-Ionen-Technik: „Lithium-Ionen-Batterien haben den Riesenvorteil, dass nicht alle Geräte zur gleichen Zeit laden müssen. Damit können wir unseren Stromverbrauch besser steuern, um Stromspitzen niedrig zu halten, was für uns kostenmässig sehr wichtig ist. Da wir zwischendrin die Pausen zum Laden nutzen, haben wir keine Einschränkungen. Es läuft wunderbar“, resümiert Selonke zufrieden.
Und auch Wechselbatterien und der Aufwand zur Pflege und zum Wechseln von Blei-Säure-Batterien entfallen. Die Mitarbeiter wurden entsprechend eingewiesen und kommen mit der neuen Technik sehr gut zurecht. Und dank des Flottenmangementsystems I_Site kann auch Guido Selonke entspannt vom PC oder Mobilgerät alle wichtigen Parameter zur Auslastung oder dem Batteriestatus verfolgen.